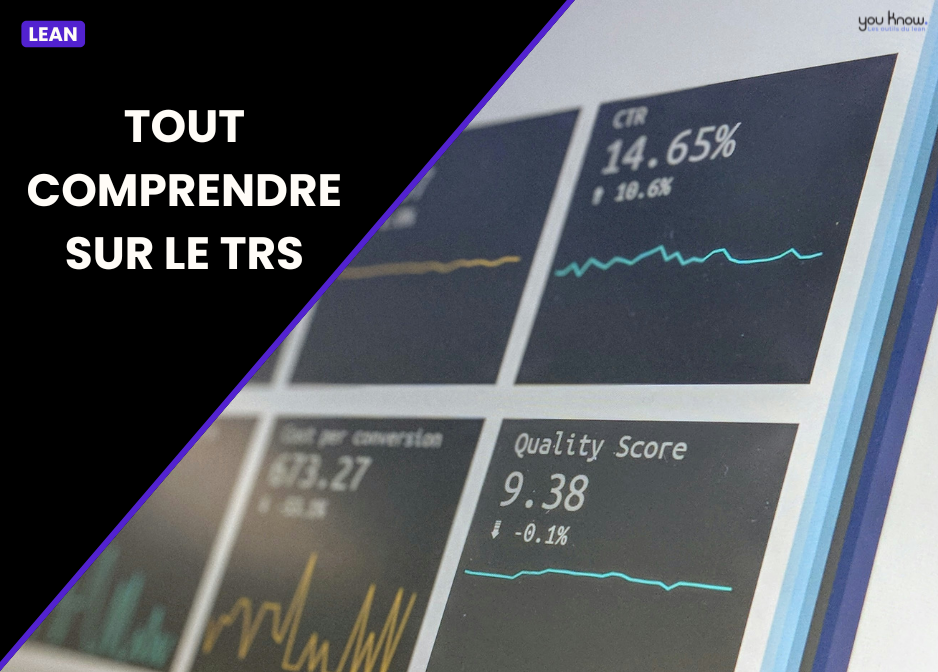
TRS (Taux de Rendement Synthétique) : Définition, exemples et calculs
|
|
Temps de lecture 14 min
|
|
Temps de lecture 14 min
Le Taux de Rendement Synthétique (TRS), appelé en anglais « Overall Equipment Effectiveness » (OEE), est un indicateur clé pour évaluer l’efficacité d’un outil de production. Il permet de mesurer la performance globale d’une machine en prenant en compte trois aspects : la disponibilité, la performance et la qualité. Cet indicateur aide à identifier les pertes et à optimiser la productivité des équipements industriels.
Sommaire
Le TRS ( taux de rendement synthétique ) sert d' outil de référence pour mesurer l' efficacité des moyens de fabrication . On peut citer la norme NF E60-182 qui encadre la méthodologie de calcul du TRS.
Il évalue le rapport entre le temps idéal de production et le temps planifié planifié, en intégrant le facteur de trois dimensions : la disponibilité, la performance et la qualité. Atteindre 100% signifierait une utilisation parfaite des moyens sans arrêt ni déperdition. Concrètement, cet outil synthétise l'occupation réelle d'une ressource productive.
Son utilité principale ? Mettre en lumière l'état de fonctionnement des machines. Grâce à lui, on peut suivre et comparer les données opérationnelles en temps réel . Son calcul résulte simplement de la multiplication des trois composantes clés (Disponibilité, Performance, Qualité). Plus le résultat approche de 100%, mieux les moyens sont exploités. Signalons qu'il s'agit d'une référence incontournable dans les démarches Lean management .
Le concept d’« usine cachée », ou Hidden Factory, est essentiel à comprendre dans l’industrie. Il désigne l’ensemble des pertes de performance qui passent souvent inaperçues dans les ateliers de production. Cela inclut les arrêts non planifiés, les ralentissements, les réglages imprévus ou encore les défauts qualité. Ces dysfonctionnements, souvent absents des tableaux de bord classiques, représentent pourtant un gisement d’amélioration majeur.
En s’attaquant à ces inefficacités, une entreprise peut augmenter sa productivité sans recourir à de lourds investissements. Optimiser ces zones de gaspillage, même de manière marginale, permet de réduire les coûts, d’améliorer les délais et la qualité, tout en renforçant la compétitivité.
Ces pertes correspondent aux MUDA, terme japonais signifiant “gaspillage”. Dans le Lean Manufacturing, on identifie 7 types de MUDA qui freinent la productivité sans générer de valeur pour le client :
1. Surproduction : Produire plus que la demande réelle. Cela augmente les coûts de stockage, crée un risque d’obsolescence et cache les problèmes de flux.
2. Temps d’attente : Machines ou opérateurs en attente de matières, d’informations ou de maintenance, ce qui crée des interruptions et ralentit la production.
3. Transports inutiles : Déplacements excessifs des matériaux ou produits, souvent causés par une mauvaise organisation de l’atelier ou un flux de production non optimisé.
4. Processus inutiles : Opérations ou étapes de fabrication qui n’apportent pas de valeur ajoutée, souvent dues à des pratiques obsolètes ou des exigences mal définies.
5. Stocks excessifs : Accumulation de matières premières, en-cours ou produits finis, qui immobilisent du capital, augmentent les coûts de stockage et masquent les inefficacités.
6. Mouvements inutiles : Déplacements ou gestes inutiles des opérateurs, causés par une mauvaise ergonomie ou un agencement inadapté, augmentant la fatigue et le risque d’erreurs.
7. Défauts de fabrication : Produits non conformes nécessitant retouche, rebuts ou rappels, avec un impact direct sur les coûts, la satisfaction client et la qualité mesurée dans le TRS.
Le Taux de Rendement Synthétique (TRS), ou Overall Equipment Effectiveness (OEE), est l’outil clé pour révéler ces pertes. Il met en lumière les axes de progrès en mesurant la disponibilité, la performance et la qualité des équipements. Bien plus qu’un simple indicateur, le TRS est un levier puissant pour engager les équipes dans une démarche d’amélioration continue.
Pour bien comprendre le taux de rendement synthetique , il est essentiel de maîtriser les différents temps d'états qui le composent. Voyons comment ces éléments s'articulent concrètement.
Temps Total (TT):
C’est la durée complète sur laquelle un équipement pourrait théoriquement être utilisé. Généralement, cela correspond à 24 heures par jour ou 168 heures sur une semaine, que la machine fonctionne ou soit à l’arrêt.
👉 Formule : TT = Temps total sur la période considérée.
Temps d'Ouverture (TO) :
Il représente le créneau où la machine est censée être en fonctionnement selon le planning de production. Par exemple, si l’atelier tourne en 2 équipes de 8 heures, le temps d’ouverture sera de 16 heures.
👉 Formule : To = TT - Périodes prévues de fermeture.
Temps Requis (TR) :
C’est le temps pendant lequel l’équipement est réellement programmé pour produire, en tenant compte des arrêts planifiés (pauses, maintenance préventive, nettoyages, etc.).
👉 Formule : Tr = To - Interruptions planifiées.
Temps de Fonctionnement (TF) :
Il correspond au temps réel où la machine tourne, en soustrayant les arrêts imprévus comme les pannes ou les temps de réglage inattendus.
👉 Formule : Tf = Tr - Arrêts non planifiés.
Temps Net (TN) :
Il s’agit du temps durant lequel l’équipement produit à la cadence de référence. Si la vitesse de production est plus lente que prévu, on soustrait ces écarts pour obtenir le temps net.
👉 Formule : Tn = Tf - Pertes de cadence.
Temps Utile :
C’est le temps consacré à produire des pièces conformes, sans défauts ni retouches. Si une partie de la production est rebutée, cela vient réduire ce temps.
👉 Formule : Tu = Tn - Temps consacré à la non-qualité.
On passe d’un potentiel théorique de 24h à un temps utile réel qui reflète la production de bonne qualité. Chacune de ces étapes permet d’identifier les sources de perte et d’optimiser l’utilisation des équipements.
Maintenant que l'on a compris comment se décompose les temps d'états selon la norme on va utiliser une méthode un peu plus simple pour le calculer.
lle exprime la proportion de temps où la machine est réellement en capacité de produire, par rapport à la durée pendant laquelle elle était censée fonctionner. Toute interruption vient impacter ce ratio.
Arrêts non planifiés
Ce sont les imprévus qui stoppent brutalement la production :
- Pannes mécaniques ou électriques : défaillance des équipements ou coupures de courant.
- Manque de matières premières : rupture d’approvisionnement empêchant la production.
- Problèmes qualité critiques : nécessitant des vérifications ou des retouches sur la chaîne.
- Accidents ou incidents de sécurité : intervention immédiate pour protéger le personnel.
Arrêts planifiés
Ce sont des interruptions prévues dans l’organisation de la production :
- Maintenance préventive : pour garantir la fiabilité des machines.
- Changements de série ou de format : adaptation des équipements à une nouvelle production.
- Inventaires physiques : contrôle des stocks de matières premières et de produits finis.
- Formations des opérateurs : développement des compétences des équipes en dehors des horaires de production.
- Mises à jour des logiciels industriels : pour optimiser les systèmes de pilotage ou de supervision.
La performance représente la capacité d’un équipement à produire à sa vitesse nominale, c’est-à-dire au rythme optimal défini par le standard de production. Si la cadence est ralentie, même légèrement, la productivité s’en trouve affectée. Deux types de perturbations influencent cette composante : les micro-arrêts et les ralentissements.
Micro-arrêts
Ce sont de courtes interruptions qui, prises individuellement, paraissent insignifiantes, mais cumulées sur une période, génèrent une perte de temps notable. Exemples :
- Réglages ponctuels : Ajustements rapides pour corriger de petits écarts sur la machine.
- Nettoyages express : Interventions brèves pour garantir la propreté de l’équipement ou de la zone de travail.
- Changements d’outillage : Remplacement rapide d’un outil usé ou endommagé sans arrêt prolongé de la ligne.
- Micro-pannes : Dysfonctionnements momentanés résolus rapidement par l’opérateur.
- Contrôles qualité spontanés : Vérifications de conformité réalisées en cours de production pour éviter les dérives.
Ralentissements
Ils traduisent un rythme de production inférieur à la capacité maximale de l’équipement. Ces pertes sont souvent moins visibles que les arrêts, mais tout aussi coûteuses :
- Problèmes de coordination : Désynchronisation entre différentes étapes de production, créant des attentes ou des bouchons.
- Apprentissage en situation réelle : Formation du personnel directement sur la ligne, ralentissant temporairement le flux.
- Vitesse réduite des équipements : Machines opérant en dessous de leur cadence cible, par sécurité ou précaution.
- Délais d’approvisionnement : Matières premières livrées en retard, forçant la ligne à ralentir en attendant le réapprovisionnement.
- Hétérogénéité des compétences : Différences de maîtrise technique entre opérateurs entraînant des variations dans la vitesse d’exécution.
La qualité correspond à la proportion de produits répondant aux exigences de conformité par rapport au volume total fabriqué. Cette mesure prend en compte toutes les pertes liées à la fabrication de pièces défectueuses, qu’elles soient détectées pendant la production ou dès le démarrage.
Défauts en cours de production
Ces problèmes surviennent pendant la fabrication et peuvent entraîner des rebuts ou des retouches :
- Anomalies de fabrication : défauts d’aspect, dimensions hors tolérances ou assemblages incorrects.
- Non-respect des spécifications : écarts par rapport aux standards techniques ou aux attentes du client.
- Mauvais étalonnage des machines : équipements mal réglés générant une variabilité de la qualité.
- Pollution ou contamination : introduction de corps étrangers, notamment dans les secteurs sensibles (agroalimentaire, pharmaceutique).
- Outillage usé ou défectueux : altérant la précision et la qualité du produit fini.
Défauts au démarrage de la production
Ils apparaissent principalement lors des mises en route de ligne ou de changement de série :
- Réglages inadaptés : erreurs dans les paramètres machine au démarrage.
- Temps de montée en régime : phase initiale où les machines atteignent leur stabilité, provoquant des produits non conformes.
- Défauts initiaux fréquents : les premiers articles fabriqués nécessitent souvent des ajustements avant d’atteindre la qualité attendue.
- Problèmes sur les matières premières : mauvais lots, qualité insuffisante ou erreurs d’approvisionnement au démarrage.
- Manque de formation ou d’expérience des opérateurs : erreurs humaines sur les premières séries, avant montée en compétence.
L’objectif est de maximiser la production de pièces conformes dès le premier coup. En réduisant ces sources de non-qualité, on améliore directement la performance globale et on réduit les gaspillages.
Prenons un cas où l’objectif de production est fixé à 1 000 pièces pour une journée, mais au final, 800 unités sont réellement fabriquées.
Le calcul rapide du TRS est alors :
TRS = 800 / 1 000 = 80%
Cette approche est basique et donne une vision globale de la performance. Toutefois, elle ne permet pas d’analyser les causes des pertes (temps d’arrêt, cadence réduite, défauts de qualité).
Exemple détaillé avec la méthode complète (Disponibilité x Performance x Qualité)
Contexte :
-> La machine est censée tourner 16 heures par jour (temps d’ouverture).
-> On prévoit 2 heures de maintenance et 2 heures d’arrêts imprévus.
1) Disponibilité
- Temps théorique disponible : 16h - 2h (planifié) = 14 heures
- Temps réellement utilisé : 14h - 2h (non-planifié) = 12 heures
Taux de disponibilité = 12h / 14h = 85,7%
2) Performance
Objectif : produire 60 pièces par heure, soit 720 pièces en 12 heures.
- Réellement produites : 680 pièces
- Taux de performance = 680 / 720 = 94,4%
3) Qualité
Sur les 680 pièces produites, 650 sont conformes.
- Taux de qualité = 650 / 680 = 95,6%
TRS final :
TRS = Disponibilité x Performance x Qualité
TRS = 85,7% x 94,4% x 95,6% = 77%
Ce résultat montre que 77% du potentiel total de la machine a été réellement transformé en production conforme. Ce type d’analyse détaillée permet d’identifier les leviers d’amélioration : réduire les arrêts, accélérer la cadence, ou améliorer la qualité.
Pour bien comprendre les leviers d'amélioration il faut décomposer les raisons des arrêts de chaque facteur. Pour ça il existe plusieurs méthodes pour suivre son TRS.
Utiliser des fiches de suivi papier et des tableaux Excel est une solution simple et accessible pour suivre la performance de vos équipements, notamment le TRS. C’est une méthode pratique pour les petites structures qui souhaitent débuter une démarche d’amélioration sans engager de gros budgets.
Concrètement, les opérateurs consignent sur des fiches les temps de production, les arrêts (prévus ou non), les quantités fabriquées et les défauts constatés. Ces données sont ensuite saisies dans un tableau Excel. Ce fichier peut calculer automatiquement les trois indicateurs clés du TRS :
• Disponibilité
• Performance
• Qualité
C’est une approche pédagogique qui permet de sensibiliser les équipes terrain à la mesure de la performance. Toutefois, elle reste manuelle et demande du temps pour consolider les informations, avec un risque d’erreurs lors de la saisie ou de l’interprétation.
Exemple pratique
Un opérateur note chaque arrêt de machine avec l’heure et la cause (panne, manque de matière, réglage…). Ces données sont regroupées en fin de poste dans un tableau Excel. L’analyse permet de visualiser les temps d’arrêt cumulés, les pertes de cadence et les rebuts. Ce suivi donne une vision claire de la journée et permet d’identifier rapidement les points à améliorer.
Cette méthode associe la collecte manuelle d’informations avec des systèmes automatisés partiels. Typiquement, des capteurs installés sur les équipements enregistrent automatiquement les périodes de fonctionnement et les arrêts. Pendant ce temps, les opérateurs saisissent manuellement des données plus qualitatives, comme les causes des défauts ou les types de pannes, directement via des interfaces simplifiées (tablettes ou bornes tactiles).
Ce mode de fonctionnement est idéal pour les entreprises de taille intermédiaire. Il combine la précision d’un suivi automatisé sur les temps machine avec la souplesse d’une intervention humaine pour qualifier les incidents. Ce compromis réduit les risques d’erreurs liés à la saisie manuelle tout en limitant l’investissement financier requis par une solution 100 % automatisée.
Les compétences nécessaires :
Pour tirer pleinement parti de ces systèmes, il est important que les équipes maîtrisent les outils informatiques de base. Une formation ciblée est souvent nécessaire pour comprendre le fonctionnement du logiciel, savoir interpréter les indicateurs clés comme la disponibilité, la performance et la qualité, et produire des rapports utiles à la prise de décision.
Avec cette approche, les données brutes issues de la production deviennent de véritables leviers d’action pour améliorer le pilotage et l’efficacité des lignes.
Pour une gestion précise et réactive de votre Taux de Rendement Synthétique, l’automatisation complète reste la solution la plus performante. Grâce à l’IIoT (Internet Industriel des Objets), les équipements sont équipés de capteurs intelligents capables de transmettre en temps réel des données critiques (vitesse, température, pression, états de fonctionnement…). Ces informations sont centralisées dans des plateformes cloud ou des systèmes MES, permettant un pilotage fin et instantané.
Fonctionnement :
- Les capteurs connectés collectent des données fiables sur l’état de vos machines.
- Les systèmes MES ou plateformes IIoT agrègent ces informations pour fournir des tableaux de bord dynamiques.
Cette approche offre une vision en temps réel sur la disponibilité des équipements, la performance de production et la qualité des produits. Le résultat : un TRS actualisé en permanence, des alertes instantanées en cas d’écart, et une réactivité maximale pour corriger les dérives.
Choisir la bonne formule pour suivre vos indicateurs clés – dont le TRS – implique d'abord d'évaluer la taille de votre structure et sa maturité en outils numériques . PME, grands groupes et sous-traitants présentent en effet des besoins distincts en gestion industrielle . Signalons que les coûts varient selon les solutions logicielles retenues, les capteurs déployés… sans négliger l'importance des formations internes pour maîtriser ces indicateurs.
Voyons maintenant les critères déterminants grâce à ce tableau comparatif , qui vous aidera à sélectionner la méthode et les outils adaptés à votre contexte :
Méthode | Précision | Investissement | Temps de mise en œuvre | Adapté pour |
---|---|---|---|---|
Manuel | Moyenne | Faible | Immédiat | Ateliers pilotes |
Semi-auto | Bonne | Modéré | 2-4 semaines | PME industrielles |
Auto | Excellente | Élevé | 3-6 mois | Grands sites automatisés |
De notre point de vue la meilleur méthode reste la semi-auto car elle permet de garder impliqué les opérateurs dans une démarche d'amélioration continue tout en ayant un coût compétitif.
Le Taux de Rendement Synthétique (TRS) est un indicateur clé pour mesurer l’efficacité d’une ligne de production, mais il peut être biaisé si certaines erreurs sont commises. Voici les pièges les plus courants et comment les éviter.
1) Sous-estimer les micro-arrêts et les ralentissements
Ces interruptions de courte durée (quelques secondes à quelques minutes) sont souvent négligées car elles paraissent insignifiantes. Pourtant, cumulées sur une journée, elles peuvent représenter une perte importante de performance. Si ces temps ne sont pas correctement relevés, la performance réelle sera surestimée.
Ce qu’il faut faire :
Mettre en place un suivi rigoureux, avec des capteurs ou une saisie précise par les opérateurs, pour enregistrer chaque arrêt, même bref.
2) Négliger la non-qualité dans le calcul
Un TRS juste doit tenir compte de toutes les pièces non conformes, qu’elles soient rebutées ou nécessitent une retouche. Si ces pertes sont ignorées, le taux de qualité sera faussé et donnera une image trop optimiste de la production.
Ce qu’il faut faire :
S’assurer que tous les défauts sont comptabilisés : rebuts, retouches, reprises, etc. Le TRS reflète la capacité à produire “du premier coup et bien fait”.
3) Utiliser le TRS comme un outil de surveillance excessive
Le TRS n’est pas conçu pour fliquer les opérateurs ! Il sert à identifier des opportunités d’amélioration et à favoriser la collaboration terrain. Une mauvaise utilisation, centrée sur le contrôle du personnel, risque de créer de la méfiance et de nuire à l’engagement des équipes.
Ce qu’il faut faire :
Adopter une démarche d’amélioration continue partagée, où chacun est acteur des résultats, sans crainte de sanction. La transparence et l’implication des opérateurs sont essentielles.
Bonnes pratiques pour un TRS fiable :
1- Former les équipes sur la collecte de données et l’importance de l’exactitude.
2- Mettre en place des outils simples mais robustes (Excel avancé, MES, capteurs IoT).
3- Organiser des revues régulières des résultats avec l’équipe de production pour identifier et corriger les biais éventuels.
👉 L’objectif n’est pas de surveiller, mais de progresser. Un TRS bien calculé devient un véritable levier pour améliorer la productivité, la qualité et la disponibilité de votre outil industriel.
Le TRS est un indicateur de performance industrielle qui mesure l’efficacité d’un équipement ou d’une ligne de production. Il prend en compte trois dimensions : Disponibilité, Performance et Qualité.
Il permet d’identifier les pertes de productivité : arrêts machines, ralentissements ou défauts qualité. C’est un outil clé pour piloter l’amélioration continue et augmenter la rentabilité.
TRS = Disponibilité × Performance × Qualité
• Disponibilité = Temps de fonctionnement réel / Temps requis
• Performance = Production réelle / Production théorique
• Qualité = Pièces conformes / Pièces produites
TRS (Taux de Rendement Synthétique) mesure l’efficacité par rapport au temps requis.
TRG (Taux de Rendement Global) prend en compte le temps total disponible, incluant les fermetures planifiées.
• Oublier les micro-arrêts
• Ignorer les pièces non conformes
• Utiliser le TRS comme outil de contrôle humain plutôt que d’amélioration collective